SM 50/40
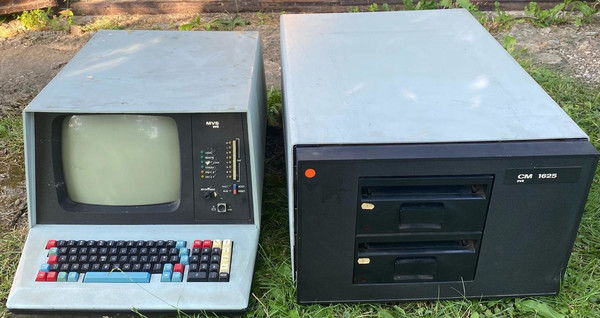
The system was gradually developed and supplemented in the following years. The SM 50/40-1 microcomputer system is designed especially for machine control. devices and equipment, in the form of a terminal station for collecting and pre-processing information and in the form of a MVS 80 Microcomputer Development System for application development.
The CM 1601 terminal connected to the system
Made 128 pcs
The processor board is designated SM 2138. The single-board microcomputer SM 50/40-1 contains a basic 8080 microprocessor, I-41 bus control in an 8-bit version and an 8-level interrupt system that allows addressing of the operating memory up to 64 KB. It also contains a built-in RAM with a capacity of 2 KB and 4 KB EPROM, one IRPS or S2 serial transmission channel, 48 TTL input-output lines, for example to implement 4 parallel IRPR input-output channels, and a timer.
- 16 KB DRAM, 640 ns cycle, 420 ns access
- 16 KB CMOS RAM backed up, 1100 ns cycle, 950 ns access
- 16 KB EPROM, 650 ns cycle, 550 ns access
- Combined memory up to 64 KB DRAM, cycle 600 ns, access 420 ns., and EPROM up to 16 KB, cycle 650 ns, access 550 ns, together for a total. 64 KB capacity
- SM 2151+SM 2154 RJ external memory on flexible disk (2 mechanisms), 2 x 256 KB, 250 Kbit/s
- SM 2143+SM 2158 RJ connection non-standard. PZ (sensor DP FS 1501, punch DP DT 105, mosaic printer C 2111, programmer PROM/EPROM memory PGM)
It uses a dual-board FDD controller based on the MH3000 architecture.
- SM 2150: 4 serial asynchronous IRPS or S2 channels
- SM 2165: 72 parallel TTL inputs/outputs
Modules of interaction with the technological process
- SM 1350: 16-channel differential low-level analog multiplexer LLM
- SM 1352: differential program. amplifier, sampling amplifier, 12bit ADC
- SM 1353: 8x 8-bit DACs with current. or back. output A 08
- SM 1354: 4x 12-bit DAC with current. or back. output A 12
- SM 1355: 48 discrete galvanically isolated DIO inputs/outputs
- SM 1356: 8 galvanically isolated CI counter inputs
- SM 1357: 32 galvanically isolated interrupt inputs II
- SM 1358: 8 galvanically isolated pulse outputs PO
- SM 1360: 32-channel differential high-level analog multiplexer HLM
- SM 2170: 32-bit math module for DP and FP, working in parallel with the CPU
Design Microcomputer Development System (MVS 80)
The development system MVS 80 was produced in two versions.
In both cases, the design of the terminal station was based on a built-in cartridge for 8 standard 2/3 SMEP boards. In addition to the boards of the CM 1601 video terminal, the processor boards, 64 KB memory, RJ external memory on a flexible disk or the control boards of the non-standard PZ emulator MVE 80 and control board of the PGM 08 type PROM/EPROM memory programmer.
MVS 80-I
The first MVS 80-I was oriented around a punched tape sensor and puncher and used punched tape as the storage medium.
The MVS 80-I development system ran under the LOS MVS 80 punched tape operating system.
MVS 80-II
The second MVS 80-II – used a floppy disk as a storage medium and used a floppy disk-based memory as an external memory.
The MVS 80-II development system worked under the DOS MVS 80 disk operating system, which also supported the work and the PGM 08 PROM/EPROM memory programmer. Macro assembler and BASIC translators were also available, for DOS MVS 80 also PL/M 80, FORTRAN 80 and PASCAL 80
Processor replacement for Z80 in SMS / SM-50/40
The connection diagram of the processor with Z80 for MVS SM50/40-1 (Ing. Stanislav Černý, c.ú.o. ORGREZ Brno) has survived.
Industry - aerated concrete production
The solution for controlling the technological nodes of the aerated concrete production was designed according to the then modern principles of the design of microcomputer systems. The goal was to improve the quality of management of technological operations and final products, to reduce the consumption of raw materials and energy, as well as to optimize the process of storage, dispatch and unloading of products based on the order plan. The control system included the following key production nodes:
- raw material mill,
- node of mixing and casting of aerated concrete mass,
- slicing node,
- autoclave station,
- distribution and consumption of electricity,
- storage, unloading and dispatch of finished products.
The system was distributed, which meant that the individual functions of the control system were spatially distributed near the respective technological devices. This solution minimized delays in data transmission and processing.
Two microcomputers SM 50/40-1, one SAPI-1 and one SM 50/50-1 were used to implement the system. Each of these microcomputers functioned as an autonomous unit that implemented control algorithms for specific nodes and shared the necessary data with other units.
The first SM 50/40-1 microcomputer
This microcomputer was used to control the raw material mill, the mixing and casting process, the cutting unit and the electrical power distribution. It also implemented communication with the slave computer SAPI-1. In the mill, he ensured the control of the dosage of raw materials based on the chemical composition of the mixture, the control of the operation of the mill and the reliability of its operation. At the mixing node, he managed the dosing of components into the mixer, calculation of the recipe, monitoring of the mixing process and casting of the mixture into molds. The slicing node included operating the mass height meter and monitoring the parameters of the sliced blocks. In the field of electricity, the system monitored the consumption of customers in the plant and optimized consumption according to agreed schemes.
The first microcomputer included two DIO modules, an AAC converter module and a multiplexer, and was equipped with 16 KB of RAM and 32 KB of EPROM. Two video terminals and a mosaic printer Consul C 2111 were used for communication.
Slave microcomputer SAPI-1
The SAPI-1 microcomputer was plugged in to handle additional tasks, such as system-wide real-time synchronization, operating the technological keyboard, display units, and other devices. It communicated with the host microcomputer via parallel transmission via 8-bit ports.
The second microcomputer SM 50/40-1
The second microcomputer focused on controlling the autoclave station and steam release. The system allowed the control of autoclave cycling including the use of the maximum amount of steam without affecting performance. It contained similar equipment to the first microcomputer, including a video terminal connected via the SM 2150 module.
Software
Both microcomputers used the ERČ 80 operating system and worked in multitasking mode. The system part of the program included the management of communication with additional devices, while the technological part implemented control algorithms for individual nodes. The programs were structured into modules, some of which had a more general character and could be used in other applications.
For communication between the system and the operator, the FORMATER tool was created, which ensured the input and output of data on various devices. This tool made it possible to interrupt communication with warning messages and then resume it.
Inaccuracies/doubts related to the topic
It is most likely a copy of the iSBC80/20
Computers derived from SM 50/40
The following computers were inspired by or derived from SM 50/40:- PP-01 (ZVT B.Bystrica)
- PP-02 (ZVT B.Bystrica)
- PP-03 (ZVT B.Bystrica)
- TEXT01 (Aritma)
- SM 53/10 (ZVT Námestovo)
References
- Systémové programování v MS DOSu: 8. seminární školení k využití výpočetní techniky Olomouc říjen 1988, sekce C: Sborník. Olomouc: KV komitétu pro věd. řízení ČSVTS v Severomor. kraji, 1988. 72 s., Aplikační programové vybavení systému Mikros Robotron SM 50/40
- https://www.atpjournal.sk/rubriky/prehladove-clanky/pamatnica-k50.vyrociu-vzniku-vuvt-vziline-4.html?page_id=27107 (WebArchive)